Avoid Wasteful Finishing: Improve Processes
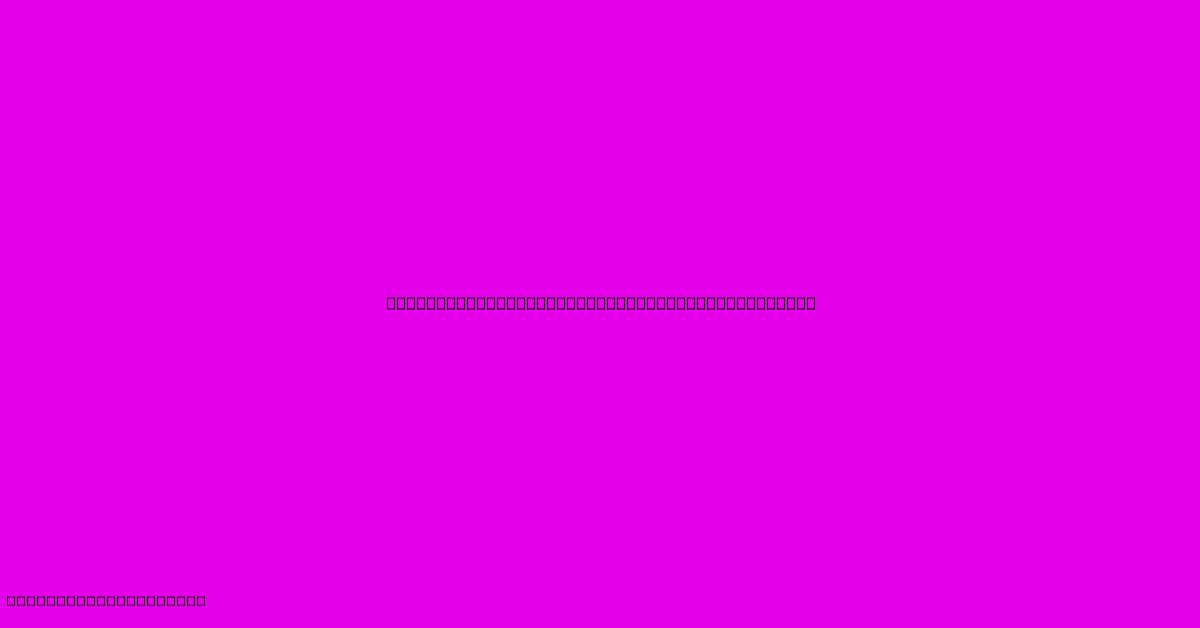
Table of Contents
Avoid Wasteful Finishing: Improve Processes for Increased Profitability
Finishing processes, while crucial for product quality and marketability, often harbor hidden inefficiencies. Understanding and eliminating these wasteful practices is paramount for boosting profitability and achieving a leaner, more competitive manufacturing operation. This article explores key areas where waste occurs in finishing and offers practical strategies for improvement.
Identifying Waste in Finishing Processes
Waste in finishing isn't always obvious. It manifests in various forms, often subtly impacting efficiency and profitability. Let's examine some common culprits:
1. Material Waste:
- Excess Material Usage: Over-application of coatings, excessive sanding, or improper material handling can lead to significant material waste. This is particularly true with expensive finishes like specialized paints or plating solutions.
- Defective Parts: Poor quality control in earlier stages can result in a high percentage of finished parts needing rework or scrapping, leading to substantial material losses.
- Inventory Management: Poor inventory control can lead to expired materials or obsolete stock, representing a significant financial loss.
2. Time Waste:
- Inefficient Processes: Outdated equipment, poorly designed workflows, or a lack of automation can dramatically increase processing times.
- Downtime: Equipment malfunctions, unplanned maintenance, or operator errors contribute to costly downtime.
- Waiting Times: Bottlenecks in the finishing process, such as insufficient buffer stock or delays in material handling, cause unnecessary waiting times.
3. Energy Waste:
- Inefficient Equipment: Outdated or poorly maintained equipment often consumes more energy than necessary.
- Excessive Heating/Cooling: Improper temperature control during the finishing process can lead to energy waste and inconsistent results.
- Unnecessary Lighting: Poor lighting design can lead to excessive energy consumption.
4. Labor Waste:
- Rework: Defects that necessitate rework consume valuable labor hours and increase costs.
- Idle Time: Waiting for materials, equipment, or instructions leads to unproductive labor time.
- Lack of Training: Inadequate training for finishing personnel can lead to errors, inefficiencies, and increased rework.
Strategies for Improving Finishing Processes and Avoiding Waste
Implementing the following strategies can significantly reduce waste and improve your finishing processes:
1. Optimize Material Usage:
- Precise Application Techniques: Invest in technology that ensures precise application of coatings, reducing overspray and material waste.
- Improved Material Handling: Implement efficient material handling systems to minimize spills and damage.
- Regular Maintenance: Maintain equipment regularly to prevent leaks and ensure optimal performance.
2. Streamline Workflows:
- Process Mapping: Analyze the entire finishing process to identify bottlenecks and inefficiencies.
- Automation: Automate repetitive tasks wherever possible to increase speed and consistency.
- Lean Manufacturing Principles: Implement lean manufacturing principles, such as 5S, to eliminate waste and improve workflow.
3. Enhance Equipment and Technology:
- Invest in Modern Equipment: Upgrade to energy-efficient equipment and tools.
- Regular Maintenance: Establish a preventative maintenance schedule to minimize downtime and extend equipment lifespan.
- Implement Monitoring Systems: Use real-time monitoring systems to track energy consumption and identify areas for improvement.
4. Empower Your Workforce:
- Comprehensive Training: Provide thorough training to your finishing personnel to improve skills and reduce errors.
- Employee Empowerment: Encourage employee suggestions for process improvement.
- Regular Performance Reviews: Implement regular performance reviews to track efficiency and identify areas needing improvement.
Measuring the Impact of Improvements
Tracking key metrics is vital to demonstrating the success of implemented changes. Consider monitoring:
- Material usage per unit: Track material consumption to identify areas where reductions can be achieved.
- Production time per unit: Monitor cycle times to measure improvements in efficiency.
- Energy consumption: Track energy usage to assess the impact of energy-saving measures.
- Defect rates: Monitor defect rates to demonstrate improvements in quality control.
By implementing these strategies and consistently monitoring key performance indicators, businesses can significantly reduce wasteful practices in their finishing processes, leading to increased profitability and a more competitive edge. Remember that continuous improvement is key; regularly assess your processes and adapt your strategies as needed.
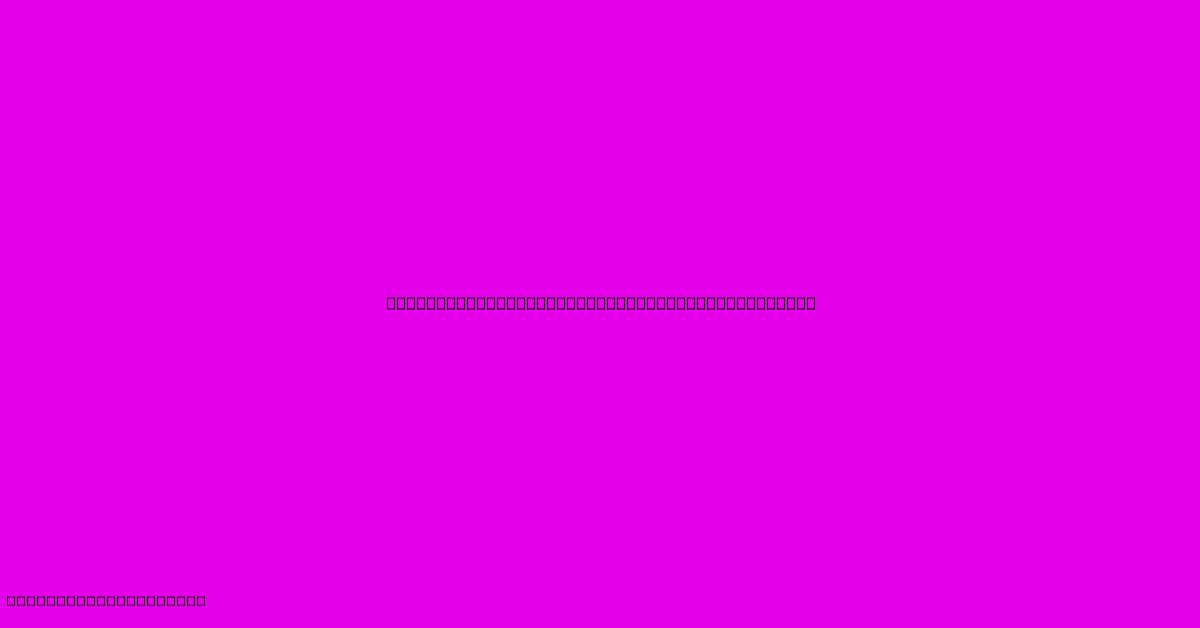
Thank you for visiting our website wich cover about Avoid Wasteful Finishing: Improve Processes. We hope the information provided has been useful to you. Feel free to contact us if you have any questions or need further assistance. See you next time and dont miss to bookmark.
Featured Posts
-
Cushions For Furniture
Feb 17, 2025
-
Kerrington 60 Inch Electric Fireplace
Feb 17, 2025
-
When Does White Lotus Season 3 Air
Feb 17, 2025
-
Freestanding Gas Fireplace Indoor
Feb 17, 2025
-
Best Craft Furniture Inc
Feb 17, 2025