End Wasteful Finishing: Boost Efficiency
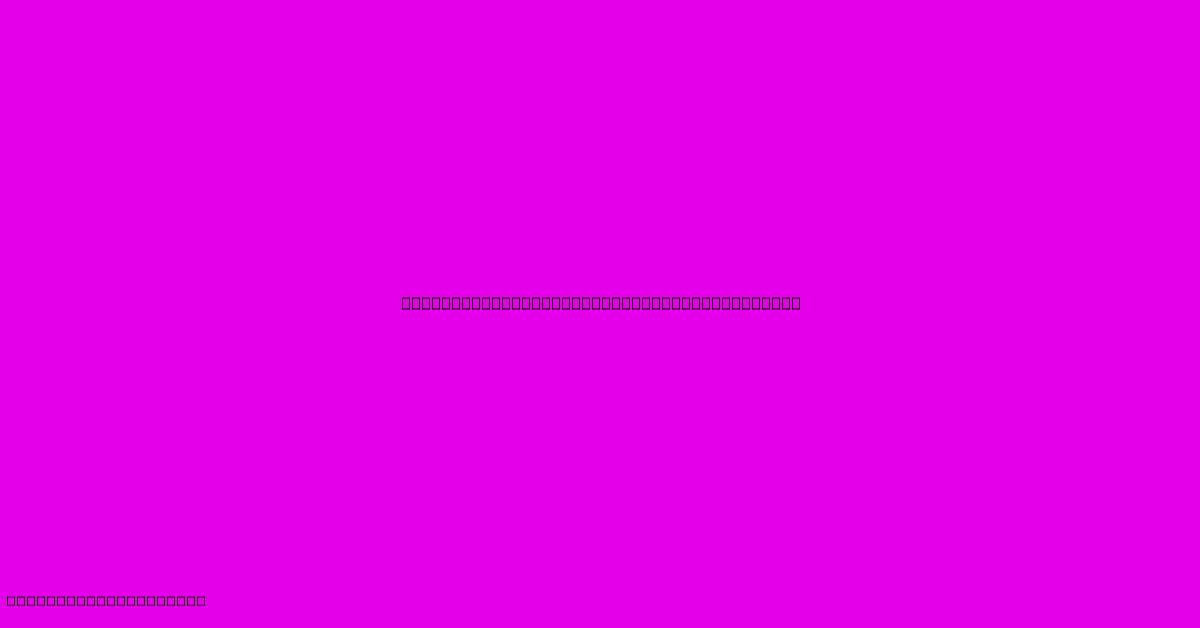
Table of Contents
End Wasteful Finishing: Boost Efficiency and Profitability
Finishing processes are crucial for manufacturing, but often a source of significant waste. This impacts not only your bottom line but also your environmental responsibility. This article explores strategies to minimize waste and maximize efficiency in your finishing operations, boosting both your profitability and your sustainability efforts.
Identifying Wasteful Practices in Finishing
Before implementing improvements, it's crucial to identify where the waste lies. Common culprits include:
-
Material Waste: Excess material usage, improper cutting, and scrap generation are major contributors. Analyze your material consumption rates and identify areas where optimization is possible. Consider techniques like nesting to minimize material usage in cutting processes.
-
Energy Waste: Inefficient equipment, prolonged processing times, and inadequate insulation contribute to high energy consumption. Regular equipment maintenance, process optimization, and energy-efficient equipment upgrades can significantly reduce your energy footprint and costs.
-
Time Waste: Downtime due to equipment malfunction, inefficient workflows, and poorly trained staff lead to lost productivity and increased costs. Implementing a robust preventative maintenance schedule and investing in employee training are key to reducing time waste.
-
Labor Waste: Inefficient processes and a lack of automation can lead to unnecessary labor costs. Analyze your workflows and explore opportunities for automation or streamlining to optimize labor efficiency.
-
Defect Waste: Products with defects require rework or disposal, resulting in significant losses. Implementing robust quality control measures throughout the finishing process can drastically reduce defect rates.
Strategies to Minimize Waste and Boost Efficiency
Implementing these strategies can significantly improve your finishing processes:
1. Optimize Your Processes
- Lean Manufacturing Principles: Adopt lean manufacturing principles like 5S (Sort, Set in Order, Shine, Standardize, Sustain) to eliminate waste and improve workflow efficiency.
- Value Stream Mapping: Map your entire finishing process to identify bottlenecks and areas for improvement.
- Process Standardization: Standardize processes to ensure consistency and reduce variability, minimizing errors and waste.
2. Invest in Modern Equipment
- Automated Systems: Explore automated systems for tasks like cutting, sanding, and finishing to improve efficiency and reduce labor costs.
- Energy-Efficient Equipment: Invest in energy-efficient equipment to reduce your energy consumption and operating costs.
- Precision Equipment: Accurate and precise equipment reduces material waste and improves product quality.
3. Improve Material Management
- Inventory Control: Implement robust inventory control systems to minimize material waste and storage costs. Implement a Just-in-Time (JIT) inventory system to reduce storage space and obsolescence.
- Material Selection: Choose sustainable and recyclable materials whenever possible to reduce your environmental impact.
- Waste Recycling: Implement a comprehensive recycling program to recover and reuse valuable materials from the finishing process.
4. Enhance Employee Training
- Proper Training: Provide comprehensive training to your employees on efficient finishing techniques, proper equipment usage, and safety procedures.
- Continuous Improvement: Encourage continuous improvement initiatives and empower employees to identify and suggest solutions for waste reduction.
5. Implement Robust Quality Control
- Regular Inspections: Implement regular inspections at each stage of the finishing process to identify and correct defects early on.
- Statistical Process Control (SPC): Utilize SPC techniques to monitor and control process variability, minimizing defects and waste.
Measuring Success and Continuous Improvement
Regularly track key performance indicators (KPIs) to measure the success of your waste reduction initiatives. These KPIs might include:
- Material usage per unit
- Energy consumption per unit
- Defect rate
- Production time per unit
- Waste generation
By continuously monitoring these KPIs and adapting your strategies, you can ensure ongoing improvements in efficiency and profitability.
Conclusion: A Sustainable Path to Profitability
Ending wasteful finishing practices isn't just about saving money; it's about building a more sustainable and responsible business. By implementing the strategies outlined above, you can significantly reduce waste, boost efficiency, and enhance your bottom line while contributing to a greener future. The journey to a more efficient finishing process is an ongoing one, requiring commitment and continuous improvement. But the rewards—both financial and environmental—are substantial.
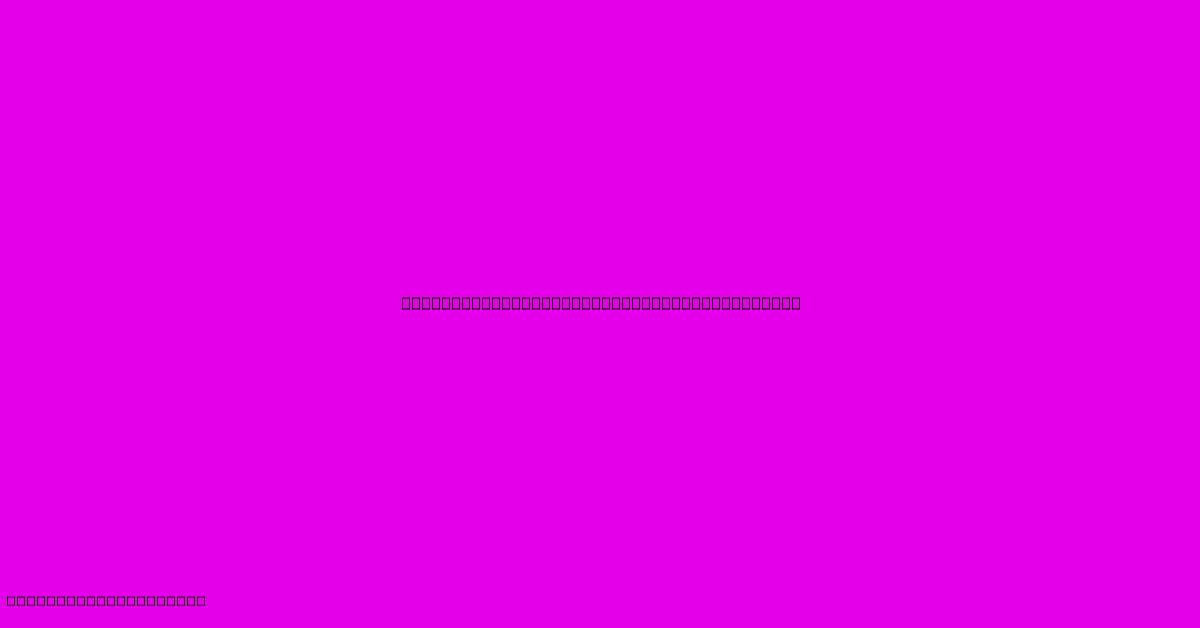
Thank you for visiting our website wich cover about End Wasteful Finishing: Boost Efficiency. We hope the information provided has been useful to you. Feel free to contact us if you have any questions or need further assistance. See you next time and dont miss to bookmark.
Featured Posts
-
Fireplace Store Chattanooga
Feb 17, 2025
-
Match Report Chelsea 2 1 Everton Analysis
Feb 17, 2025
-
White Lotus Season 3 Release Date
Feb 17, 2025
-
Coastal Ceiling Fans With Lights
Feb 17, 2025
-
Replace Gas Log Fireplace
Feb 17, 2025