Furniture Logistics
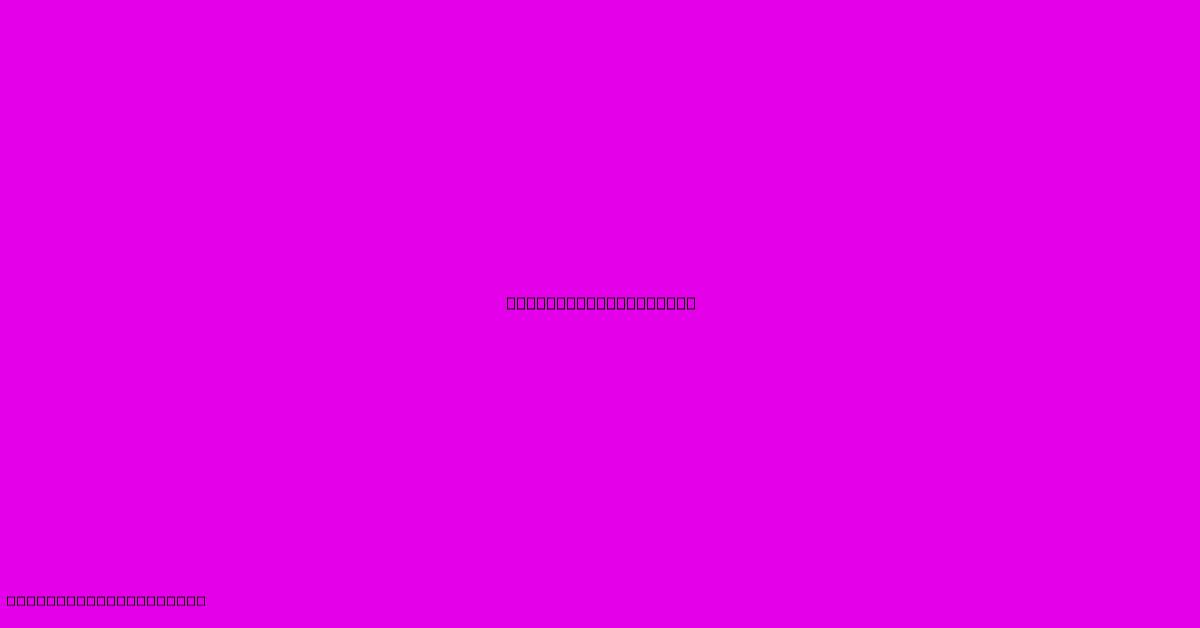
Table of Contents
Furniture Logistics: A Comprehensive Guide for Smooth Operations
Furniture logistics is a specialized field requiring meticulous planning and execution. Unlike other goods, furniture is often bulky, fragile, and requires specific handling to avoid damage. This comprehensive guide delves into the key aspects of furniture logistics, from warehousing and transportation to last-mile delivery and crucial considerations for success.
Understanding the Unique Challenges of Furniture Logistics
The furniture industry presents unique logistical challenges that differentiate it from other sectors. Key issues include:
- Size and Weight: Furniture items are often oversized and heavy, requiring specialized equipment and transportation methods. This impacts warehousing space needs and transportation costs significantly.
- Fragility: Many furniture pieces are fragile and susceptible to damage during transit. Careful packaging, handling, and transportation are crucial to minimize breakage and returns.
- Assembly: Some furniture requires assembly upon delivery, adding a layer of complexity to the logistics process. This necessitates skilled delivery personnel or clear assembly instructions for the customer.
- White-Glove Service: High-end furniture often demands white-glove service, encompassing careful delivery, unpacking, assembly, and placement within the customer's home. This requires specialized training and expertise.
- Reverse Logistics: Managing returns and damaged goods in the furniture industry requires efficient reverse logistics processes to minimize costs and maintain customer satisfaction.
Key Aspects of Furniture Logistics Management
Effective furniture logistics relies on several core components:
1. Warehousing and Inventory Management
Efficient warehousing is crucial. Consider:
- Space Optimization: Maximize storage space using racking systems and efficient layout to accommodate diverse furniture sizes and shapes.
- Inventory Tracking: Implement a robust inventory management system to track stock levels, monitor movement, and prevent stockouts or overstocking.
- Damage Prevention: Employ protective measures within the warehouse to minimize damage during storage, including proper stacking and climate control for sensitive materials.
2. Transportation and Freight
Choosing the right transportation method is paramount. Options include:
- Full Truckload (FTL): Ideal for large orders or when time sensitivity is crucial.
- Less-Than-Truckload (LTL): Cost-effective for smaller shipments but may increase transit times.
- Specialized Carriers: Necessary for oversized or exceptionally fragile furniture, requiring specialized vehicles and secure transport.
Optimizing Transportation Routes: Employ route optimization software to minimize fuel consumption, reduce transit times, and enhance overall efficiency.
3. Last-Mile Delivery and Customer Experience
The final leg of the journey is critical for customer satisfaction. Key factors include:
- Delivery Scheduling: Provide customers with flexible delivery windows and real-time tracking updates.
- White-Glove Service (if applicable): Ensure professional delivery personnel who handle furniture with care, assemble if needed, and remove all packaging.
- Damage Claims and Returns: Establish a clear process for handling damaged goods or returns, ensuring a smooth and fair resolution for the customer.
4. Technology and Automation in Furniture Logistics
Leveraging technology can streamline operations and improve efficiency:
- Transportation Management Systems (TMS): Optimize routing, track shipments, and manage carrier communications.
- Warehouse Management Systems (WMS): Control inventory levels, track stock movement, and direct warehouse operations.
- Route Optimization Software: Plan efficient delivery routes, minimizing travel time and fuel costs.
Strategies for Success in Furniture Logistics
- Invest in robust technology: Implementing advanced logistics software significantly enhances efficiency.
- Build strong relationships with carriers: Secure reliable transportation partners to ensure timely and efficient deliveries.
- Prioritize customer service: Excellent customer service fosters loyalty and positive word-of-mouth referrals.
- Implement effective quality control: Minimize damage and returns through proper handling and packaging procedures.
- Stay updated on industry trends: Keep abreast of the latest innovations and technologies to maintain a competitive edge.
By effectively addressing the unique challenges and implementing these strategies, furniture businesses can optimize their logistics operations, reduce costs, enhance customer satisfaction, and achieve sustainable growth within a competitive market. The furniture logistics landscape is ever-evolving, so continuous adaptation and improvement are essential for long-term success.
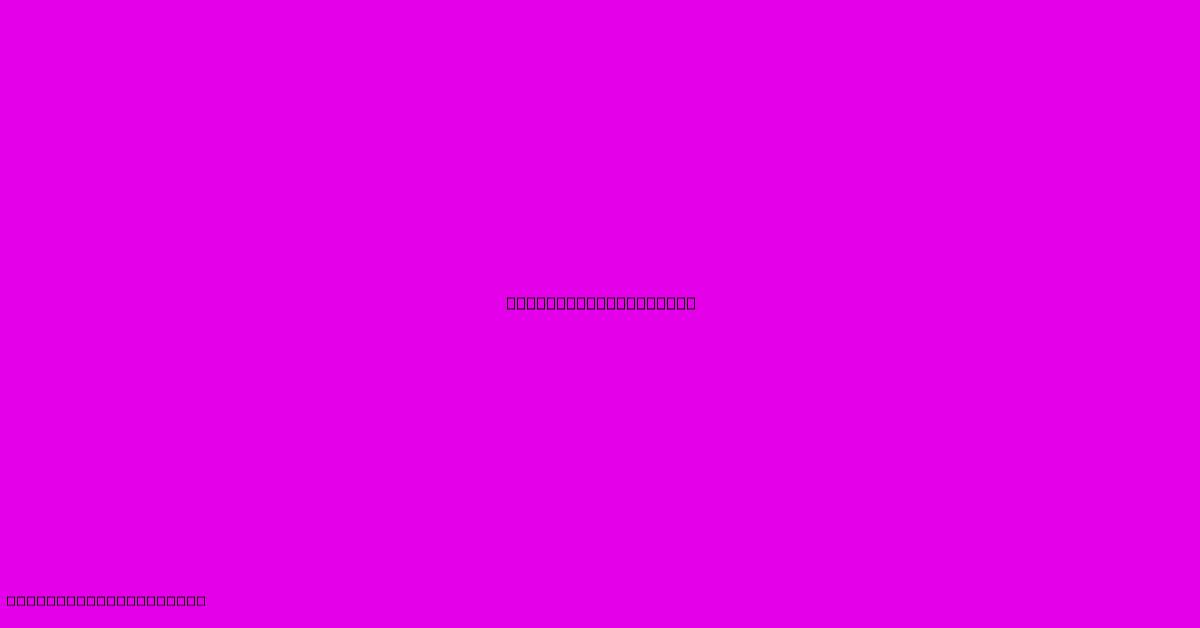
Thank you for visiting our website wich cover about Furniture Logistics. We hope the information provided has been useful to you. Feel free to contact us if you have any questions or need further assistance. See you next time and dont miss to bookmark.
Featured Posts
-
Bathroom Remodel Stafford Va
Feb 03, 2025
-
Fans Weep Boyzone Docs Final Scene
Feb 03, 2025
-
Bathroom Vanities Houston Tx
Feb 03, 2025
-
Dining Room Bench Seat
Feb 03, 2025
-
Watch 2025 Grammys Cable Streaming Guide
Feb 03, 2025