Furniture Molds
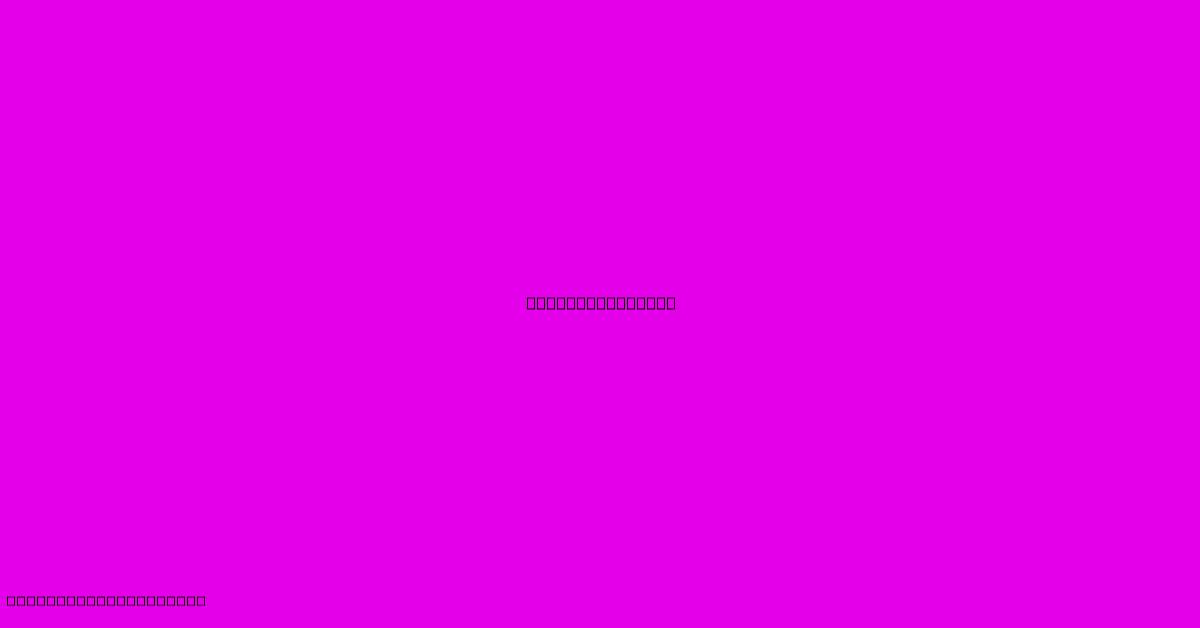
Table of Contents
Furniture Molds: The Unsung Heroes of Modern Furniture Manufacturing
Furniture molds, often unseen but incredibly important, are the backbone of many modern furniture production processes. They're the tools that shape the pieces we use daily, from the curves of a comfortable chair to the clean lines of a modern table. Understanding furniture molds, their types, and their impact on the furniture industry is key to appreciating the craftsmanship and technology behind our everyday objects. This comprehensive guide will delve into the world of furniture molds, exploring their various applications and considerations for both manufacturers and consumers.
Types of Furniture Molds: A Diverse Landscape
The world of furniture molds is surprisingly diverse, catering to a wide range of materials and manufacturing techniques. Let's explore some key types:
1. Injection Molding for Plastics and Composites:
This is a dominant force in the production of modern furniture, particularly for plastic chairs, tables, and outdoor furniture. Injection molding uses high pressure to inject molten plastic or composite material into a precisely engineered mold cavity. This allows for high-volume production of identical pieces with intricate detail and consistent quality. Keywords: injection molding, plastic furniture molds, composite furniture molds, high-pressure molding, mass production.
2. Rotational Molding for Large Hollow Pieces:
Rotational molding, also known as rotomolding, is ideal for creating large, hollow furniture pieces like storage bins, kayaks, and even some types of chairs. The process involves rotating a mold filled with powdered plastic or resin until it melts and evenly coats the interior surface. This method excels at producing durable, seamless furniture with thick walls. Keywords: rotomolding, rotational molding, hollow furniture molds, large furniture molds, durable furniture.
3. Vacuum Forming for Thermoplastics:
Vacuum forming is a versatile technique used for shaping thermoplastic sheets into various forms. A heated plastic sheet is draped over a mold, and a vacuum draws the softened plastic down to conform to the mold's shape. This method is often used for creating simple, curved furniture pieces or components. Keywords: vacuum forming, thermoplastic molds, furniture component molds, sheet molding, vacuum forming molds.
4. Compression Molding for Specialized Applications:
Compression molding involves placing material into a heated mold and applying pressure to shape it. This technique is less common in mass furniture production but is used for specialized applications where high strength and precision are required, such as in the production of certain types of high-end chairs or tabletops. Keywords: compression molding, high-pressure molding, specialized furniture molds, high-strength furniture.
Material Considerations for Furniture Molds:
The choice of mold material is critical and depends heavily on the manufacturing process and the material being molded. Common mold materials include:
- Steel: Offers high durability and precision, ideal for high-volume production.
- Aluminum: Lighter than steel, offering faster cycle times in injection molding.
- Silicone: Flexible and versatile, suitable for complex shapes and smaller productions.
The Impact of Furniture Molds on Design and Production:
Furniture molds have profoundly impacted both furniture design and manufacturing. The ability to create complex shapes with high precision and repeatability has led to innovative designs and mass production capabilities that were previously unimaginable. This has resulted in:
- Lower costs: High-volume production via molding keeps prices down for consumers.
- Consistent quality: Molds ensure consistent product quality, reducing defects.
- Innovative designs: The capabilities of molding allow designers to create more intricate and innovative furniture.
Choosing the Right Furniture Mold: Factors to Consider
For manufacturers, selecting the right furniture mold involves careful consideration of various factors:
- Production volume: High-volume production favors injection or rotational molding.
- Material properties: The mold material must be compatible with the furniture material.
- Design complexity: Complex shapes may require more specialized molding techniques.
- Budget: Mold creation and maintenance costs can vary significantly.
The Future of Furniture Molds: Innovation and Sustainability
The future of furniture molds is likely to be shaped by advancements in materials science, automation, and sustainability. We can expect to see more eco-friendly materials used in mold production and the development of more efficient and sustainable molding processes.
In conclusion, furniture molds are integral to the modern furniture industry, enabling the creation of diverse, affordable, and aesthetically pleasing furniture. Understanding their various types and considerations is crucial for both manufacturers and consumers alike. By staying informed about the latest advancements in molding technology, we can appreciate the craftsmanship and innovation behind the everyday furniture that surrounds us.
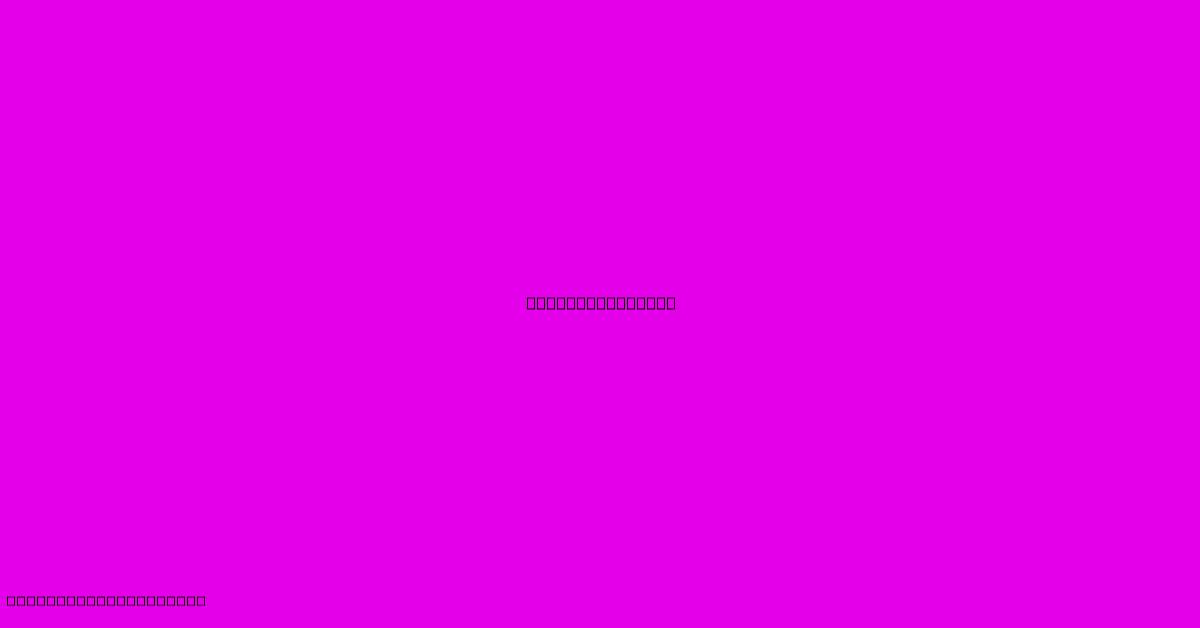
Thank you for visiting our website wich cover about Furniture Molds. We hope the information provided has been useful to you. Feel free to contact us if you have any questions or need further assistance. See you next time and dont miss to bookmark.
Featured Posts
-
Fireplace Insert For Tv Stand
Dec 18, 2024
-
Fireplace Inserts Fresno Ca
Dec 18, 2024
-
Commercial Bathroom Fan
Dec 18, 2024
-
Ceiling Fan With Wall Switch
Dec 18, 2024
-
Bathroom Shower Floor
Dec 18, 2024