Same Old, Same Old: Wasteful Finishing
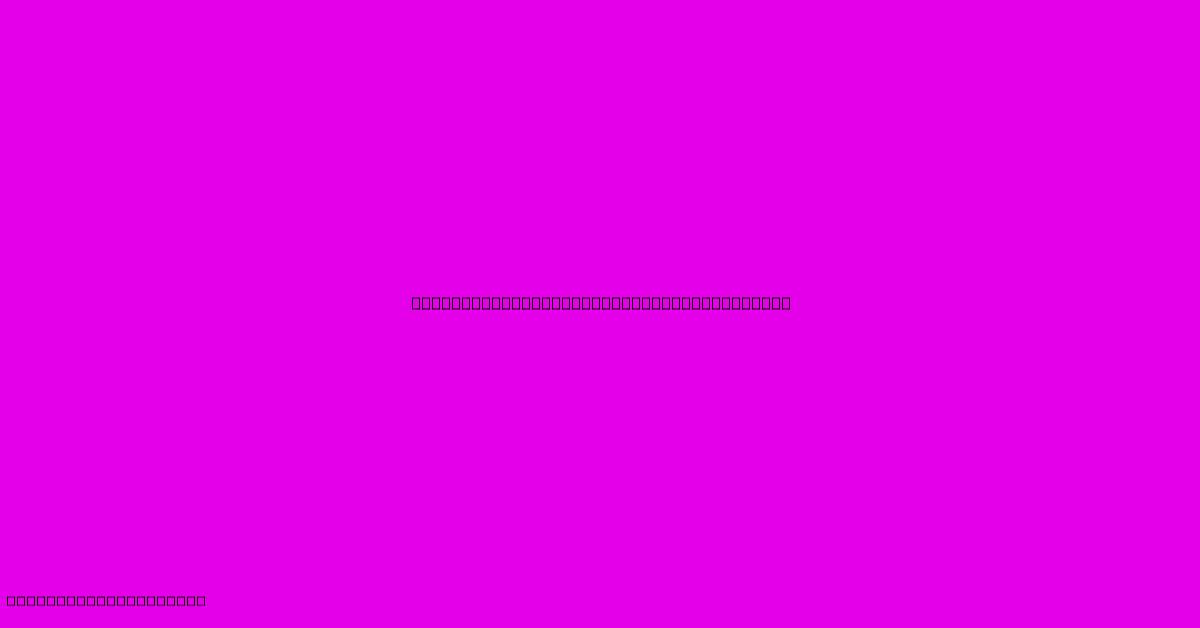
Table of Contents
Same Old, Same Old: Wasteful Finishing Practices and How to Optimize Your Processes
Are you tired of seeing perfectly good materials end up in the scrap bin? Does your finishing process feel more like a money pit than a value-added step? You're not alone. Many businesses struggle with wasteful finishing practices, losing money and impacting their environmental footprint. This article will delve into common culprits of wasteful finishing, and offer practical solutions to optimize your processes and boost your bottom line.
Identifying the Culprits of Wasteful Finishing
Waste in finishing isn't always obvious. It often sneaks in subtly, accumulating over time. Let's examine some common sources:
1. Material Waste: The Silent Thief
- Poor Cutting and Planning: Inefficient cutting techniques lead to excessive material scraps. Failing to optimize nesting software or utilizing leftover pieces creatively contributes significantly to this waste.
- Over-Application of Finishes: Applying more finish than necessary wastes product and can lead to longer drying times and potential defects. This is particularly true with paints, stains, and coatings.
- Defective Materials: Using damaged or substandard materials forces rework or discarding entire batches, resulting in significant losses. Strict quality control at the sourcing stage is crucial.
- Incorrect Material Selection: Choosing unsuitable materials for the finishing process leads to incompatibility issues, requiring costly replacements or rework.
2. Labor Waste: Time is Money
- Inefficient Processes: Poorly designed workflows and lack of automation can significantly increase labor costs and processing time.
- Rework and Corrections: Errors during the finishing stage require rework, consuming valuable time and resources. Implementing quality checks throughout the process minimizes this.
- Lack of Training: Inadequate training for finishing personnel leads to mistakes and inefficiency, increasing both material and labor waste.
3. Energy Waste: The Hidden Cost
- Excessive Energy Consumption: Outdated equipment or inefficient processes can significantly increase energy consumption, leading to higher utility bills.
- Inefficient Drying Methods: Using energy-intensive drying methods, without optimizing parameters, leads to unnecessary energy usage and longer processing times.
Strategies for Optimizing Your Finishing Process
Addressing wasteful finishing practices requires a multi-pronged approach. Here are some effective strategies:
1. Improve Material Management
- Invest in advanced nesting software: Optimize material utilization by minimizing waste during cutting and planning.
- Implement a robust quality control system: Ensure that only high-quality materials enter the finishing process.
- Embrace lean manufacturing principles: Minimize inventory and reduce waste through continuous improvement.
- Explore alternative materials: Investigate sustainable and eco-friendly alternatives that reduce waste and environmental impact.
2. Streamline Your Workflows
- Automate processes wherever possible: Automated finishing systems can improve efficiency and reduce labor costs.
- Implement standardized operating procedures: Ensure consistency and minimize errors across all finishing processes.
- Invest in operator training: Properly trained personnel are more efficient and produce higher-quality work.
- Regularly evaluate and refine your processes: Continuous improvement is key to optimizing your finishing operations.
3. Embrace Sustainable Practices
- Use water-based finishes whenever possible: Reduce VOC emissions and improve environmental sustainability.
- Recycle and reuse waste materials: Explore opportunities to reclaim and repurpose waste materials.
- Invest in energy-efficient equipment: Reduce your carbon footprint and save on utility costs.
- Monitor and track your energy consumption: Identify areas for improvement and reduce waste.
Conclusion: The Path to a More Efficient Finishing Process
Wasteful finishing practices are a significant drain on resources and profitability. By implementing the strategies outlined above, you can drastically reduce waste, improve efficiency, and boost your bottom line. Remember that a proactive, data-driven approach, coupled with a commitment to continuous improvement, is essential for achieving long-term success in optimizing your finishing processes. Don't let "same old, same old" hinder your growth – take control of your finishing operations and unlock significant gains.
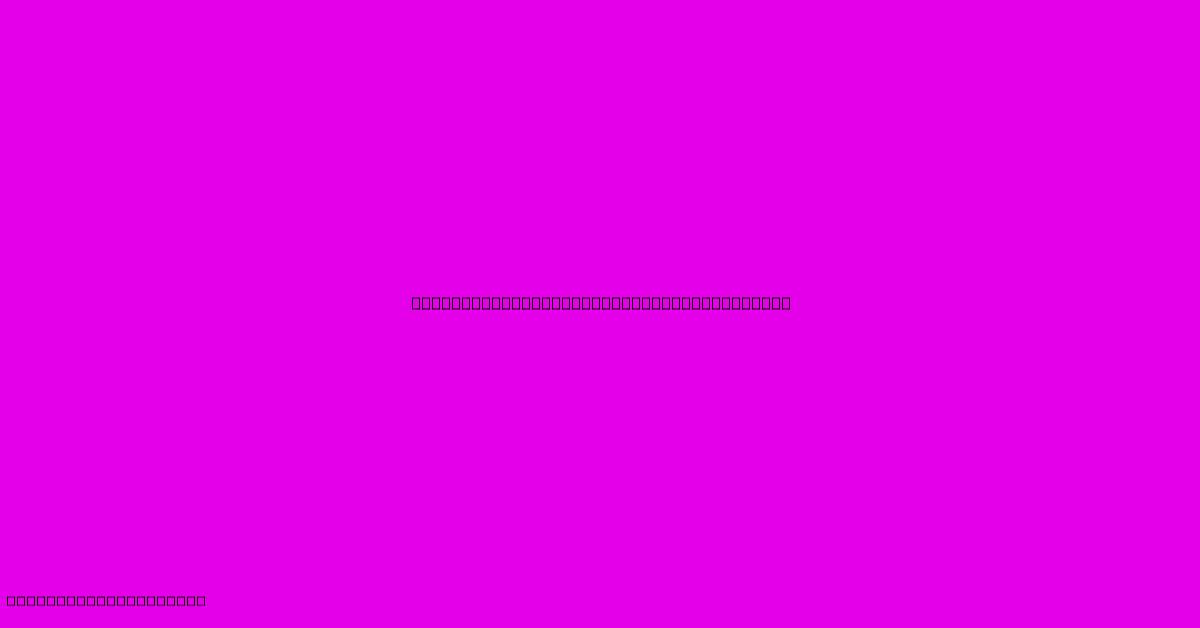
Thank you for visiting our website wich cover about Same Old, Same Old: Wasteful Finishing. We hope the information provided has been useful to you. Feel free to contact us if you have any questions or need further assistance. See you next time and dont miss to bookmark.
Featured Posts
-
Mid Century Modern Bathroom Sconce
Feb 17, 2025
-
Dallas Commercial Landscaping Ideas
Feb 17, 2025
-
Blood Moon Over Scotland Date And Time
Feb 17, 2025
-
Pendant Dining Room
Feb 17, 2025
-
Stephs Rule New Relationship
Feb 17, 2025