Wasteful Finishing? Time For A Change
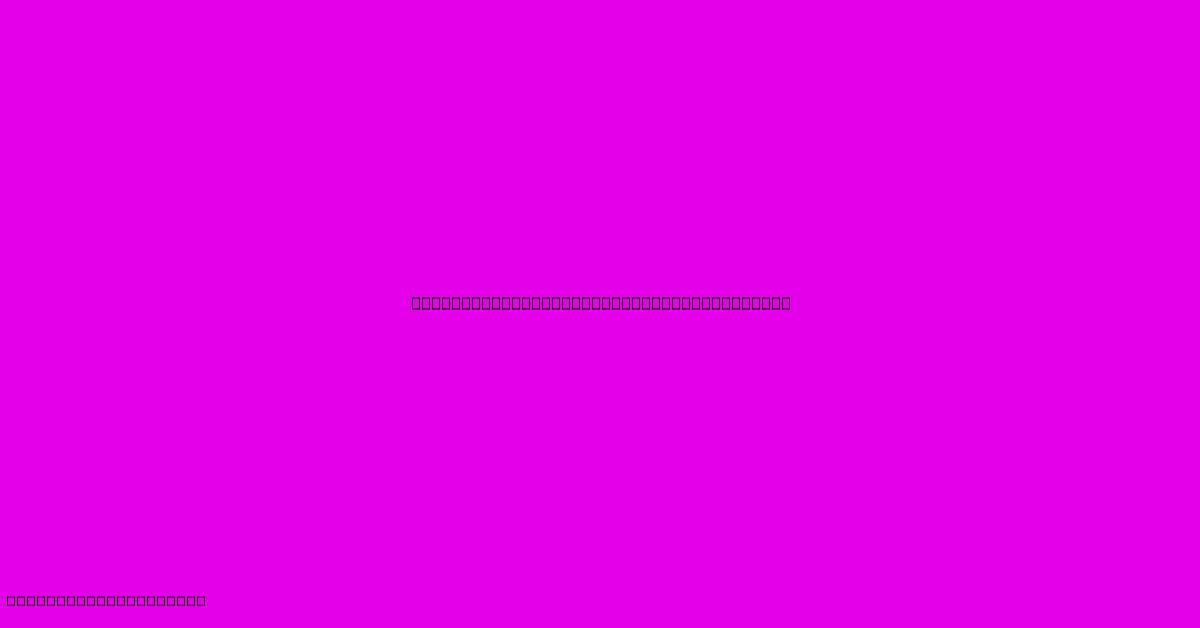
Table of Contents
Wasteful Finishing? Time for a Change
The finishing stage of any manufacturing process is crucial. It's where your product takes its final form, achieving the desired look, feel, and functionality. However, many businesses unknowingly suffer from wasteful finishing practices, leading to increased costs, reduced efficiency, and environmental concerns. This article will explore common wasteful finishing practices and offer practical solutions to help you optimize your processes and embrace a more sustainable approach.
Identifying Wasteful Finishing Practices
Before implementing changes, it's vital to pinpoint the areas where your finishing process falls short. Common culprits include:
1. Material Waste:
- Excess Material Usage: Applying more coating, paint, or other finishing materials than necessary leads to significant material waste and increased costs. This is often due to inaccurate application techniques or poorly calibrated equipment.
- Scrap and Rework: Defective parts requiring rework or complete scrapping represent a huge loss of materials and labor. This often stems from inconsistent finishing processes or inadequate quality control.
- Improper Material Handling: Poor storage and handling of finishing materials can lead to spills, damage, and ultimately, waste.
2. Time and Labor Waste:
- Inefficient Processes: Outdated equipment or poorly designed workflows can significantly increase processing times and labor costs.
- Downtime and Maintenance: Frequent equipment breakdowns or lengthy maintenance periods disrupt production and contribute to wasted time and resources.
- Overstaffing: Having more personnel than necessary for a task results in unnecessary labor costs.
3. Energy Waste:
- Inefficient Equipment: Older finishing equipment often consumes more energy than newer, more efficient models.
- Excessive Energy Use: Failing to optimize equipment settings or using inappropriate finishing techniques can lead to increased energy consumption.
Implementing a Lean Finishing Approach
Adopting a lean manufacturing philosophy in your finishing process can dramatically reduce waste and boost efficiency. Here are some key strategies:
1. Optimize Material Usage:
- Precise Application Techniques: Invest in training for your staff to ensure accurate and efficient material application. Consider using automated systems for precise dispensing and coating.
- Improved Quality Control: Implement rigorous quality control measures to minimize defects and reduce the need for rework or scrapping.
- Inventory Management: Employ efficient inventory management systems to prevent material spoilage and ensure optimal stock levels.
2. Streamline Processes:
- Process Mapping: Analyze your finishing processes to identify bottlenecks and areas for improvement. Process mapping helps visualize the flow of materials and identify inefficiencies.
- Automation: Explore opportunities for automation to reduce manual labor, improve consistency, and minimize errors.
- Equipment Upgrades: Invest in modern, energy-efficient finishing equipment to enhance productivity and reduce downtime.
3. Reduce Energy Consumption:
- Energy-Efficient Equipment: Choose equipment with high energy efficiency ratings.
- Regular Maintenance: Proper maintenance of equipment ensures optimal energy consumption and prevents unnecessary downtime.
- Improved Workspace Design: Optimize the layout of your finishing area to minimize energy waste from heating, cooling, and lighting.
Embracing Sustainability in Finishing
Beyond cost savings, sustainable finishing practices are crucial for environmental responsibility. Consider:
- Eco-Friendly Materials: Switch to water-based or solvent-free coatings to reduce VOC emissions and environmental impact.
- Waste Reduction Programs: Implement recycling and waste reduction programs to minimize landfill waste.
- Responsible Disposal: Ensure proper disposal of hazardous waste materials in accordance with environmental regulations.
Conclusion: A Path to a More Efficient and Sustainable Future
Wasteful finishing practices are costly and detrimental to the environment. By implementing the strategies outlined above, you can significantly reduce waste, improve efficiency, and contribute to a more sustainable future. The journey to a leaner, greener finishing process starts with identifying your weaknesses and committing to continuous improvement. Don't let wasteful finishing practices hinder your success—take action today and reap the rewards of a more efficient and sustainable operation.
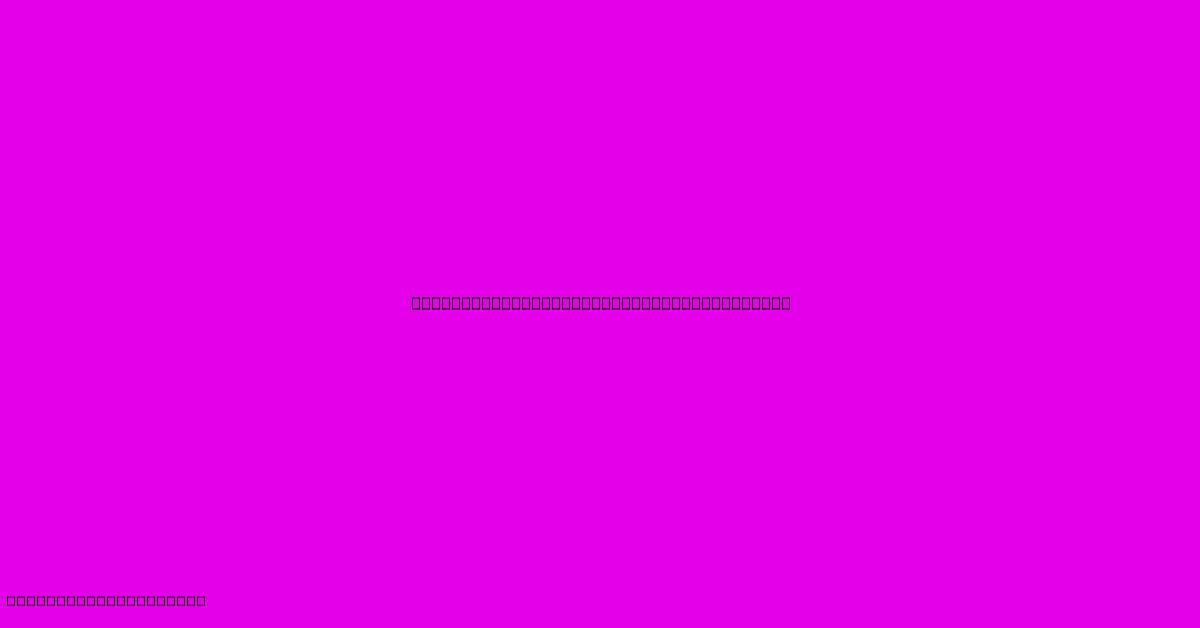
Thank you for visiting our website wich cover about Wasteful Finishing? Time For A Change. We hope the information provided has been useful to you. Feel free to contact us if you have any questions or need further assistance. See you next time and dont miss to bookmark.
Featured Posts
-
Shore Landscaping
Feb 17, 2025
-
Insects Found In Bathrooms
Feb 17, 2025
-
28x28 Patio Cushions
Feb 17, 2025
-
Antique Style Bathroom Faucets
Feb 17, 2025
-
Baftas 2024 Erivos Nail Look
Feb 17, 2025